French Solar Energy Institute Ines heeft nieuwe PV -modules ontwikkeld met thermoplastics en natuurlijke vezels in Europa, zoals vlas en basalt. De wetenschappers willen de voetafdruk van het milieu en het gewicht van zonnepanelen verminderen, terwijl ze recycling verbeteren.
Een gerecycled glazen paneel aan de voorkant en een linnen composiet aan de achterkant
Afbeelding: GD
Van PV Magazine Frankrijk
Onderzoekers van het Franse National Solar Energy Institute (INES)-een divisie van de Franse Alternative Energies and Atomic Energy Commission (CEA)-ontwikkelen zonnemodules met nieuwe biobased materialen aan de voor- en achterzijde.
"Omdat de CO2-voetafdruk en de levenscyclusanalyse nu essentiële criteria zijn geworden bij de keuze van fotovoltaïsche panelen, zal het inkoop van materialen de komende jaren een cruciaal element in Europa worden," zei Anis Fouini, de directeur van CEA-EHS , in een interview met PV -tijdschrift Frankrijk.
Aude Derrier, de coördinator van het onderzoeksproject, zei dat haar collega's hebben gekeken naar de verschillende materialen die al bestaan, om er een te vinden waarmee modulefabrikanten panelen kunnen produceren die de prestaties, duurzaamheid en kosten verbeteren, terwijl de impact van het milieu wordt verlaagd. De eerste demonstrator bestaat uit heterojunction (HTJ) zonnecellen geïntegreerd in een all-composiet materiaal.
"De voorkant is gemaakt van een met glasvezel gevuld polymeer, dat transparantie biedt," zei Derrier. "De achterkant is gemaakt van composiet op basis van thermoplastics waarin een weven van twee vezels, vlas en basalt, is geïntegreerd, wat mechanische sterkte zal bieden, maar ook een betere weerstand tegen vocht."
De vlas is afkomstig uit Noord -Frankrijk, waar het hele industriële ecosysteem al aanwezig is. Het basalt is elders in Europa afkomstig en wordt geweven door een industriële partner van INES. Dit verminderde de koolstofvoetafdruk met 75 gram CO2 per watt, vergeleken met een referentiemodule van hetzelfde vermogen. Het gewicht was ook geoptimaliseerd en is minder dan 5 kilogram per vierkante meter.
"Deze module is gericht op de PV op het dak en de bouwintegratie," zei Derrier. “Het voordeel is dat het van nature zwart van kleur is, zonder dat een achtergrondschaal nodig is. In termen van recycling, dankzij thermoplastics, die kunnen worden geremeld, is de scheiding van de lagen ook technisch eenvoudiger. ”
De module kan worden gemaakt zonder huidige processen aan te passen. Derrier zei dat het idee is om de technologie over te dragen aan fabrikanten, zonder extra investeringen.
"De enige noodzaak is om diepvriezers te hebben om het materiaal op te slaan en niet te starten van het cross-linkingsproces van hars, maar de meeste fabrikanten gebruiken tegenwoordig prepreg en zijn hier al voor uitgerust," zei ze.
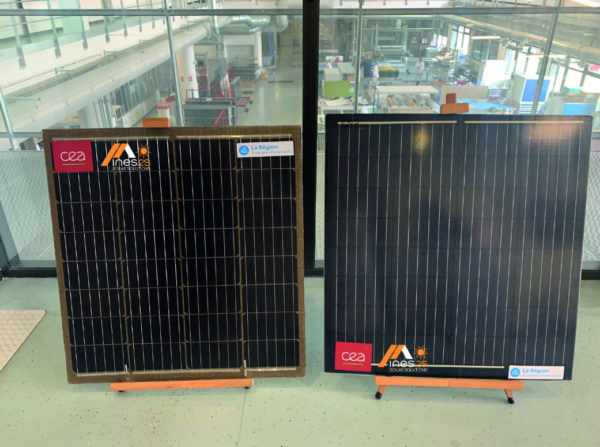
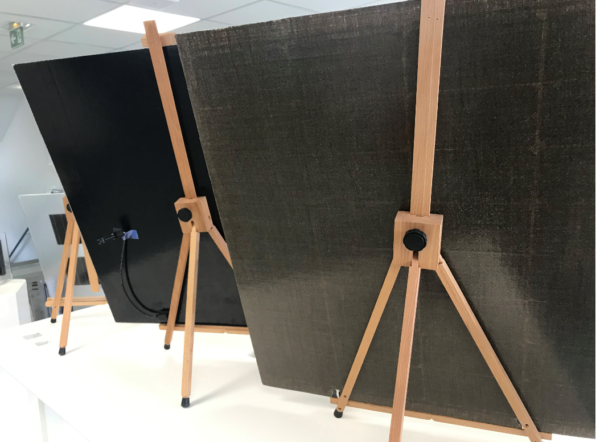
"We werkten aan de tweede levensduur van glas en ontwikkelden een module bestaande uit hergebruikte 2,8 mm glas dat afkomstig is van een oude module," zei Derrier. "We hebben ook een thermoplastisch inkapseldmiddel gebruikt waarvoor geen verknoping vereist is, waarvoor daarom gemakkelijk te recyclen is, en een thermoplastisch composiet met vlasvezel voor weerstand."
Het basaltvrije achtervlak van de module heeft een natuurlijke linnenkleur, die bijvoorbeeld esthetisch interessant kan zijn voor architecten in termen van gevelintegratie. Bovendien vertoonde het INES -berekeningstool een vermindering van 10% in de koolstofvoetafdruk.
"Het is nu noodzakelijk om de fotovoltaïsche supply chains in twijfel te trekken," zei Jouini. “Met de hulp van de regio Rhône-Alpes binnen het kader van het internationale ontwikkelingsplan, gingen we daarom op zoek naar spelers buiten de zonnesector om nieuwe thermoplastics en nieuwe vezels te vinden. We hebben ook nagedacht over het huidige laminatieproces, dat erg energie -intensief is. ”
Tussen de druk, het drukken en de koelfase duurt de laminering meestal tussen 30 en 35 minuten, met een bedrijfstemperatuur van ongeveer 150 ° C tot 160 C.
"Maar voor modules die in toenemende mate eco-ontworpen materialen bevatten, is het noodzakelijk om thermoplastics te transformeren van ongeveer 200 C tot 250 ° C, wetende dat HTJ-technologie gevoelig is voor warmte en niet meer dan 200 ° C mag overschrijden," zei Derrier.
Het onderzoeksinstituut werkt samen met de in Frankrijk gevestigde inductie-thermocompressiespecialist Roctool, om cyclustijden te verminderen en vormen te maken volgens de behoeften van klanten. Samen hebben ze een module ontwikkeld met een achtervlak gemaakt van polypropyleen-type thermoplastische composiet, waarmee gerecyclede koolstofvezels zijn geïntegreerd. De voorkant is gemaakt van thermoplastiek en glasvezel.
"Het inductie -thermocompressieproces van Roctool maakt het mogelijk om de twee voor- en achterplaten snel te verwarmen, zonder 200 ° C te moeten bereiken in de kern van de HTJ -cellen," zei Derrier.
Het bedrijf beweert dat de investering lager is en dat het proces een cyclustijd van slechts enkele minuten kan bereiken, terwijl het minder energie wordt gebruikt. De technologie is gericht op samengestelde fabrikanten, om hen de mogelijkheid te geven om delen van verschillende vormen en maten te produceren, terwijl lichtere en duurzamer materiaal wordt geïntegreerd.
Posttijd: jun-24-2022